Stud Welding Explained: How Do These Machines Work?
Are you grappling with finding a robust, efficient fastening method for your construction or manufacturing projects? Perhaps traditional bolts and nuts, or even other welding techniques, present limitations in speed, strength, or accessibility on one side. Here's the deal: stud welding offers a remarkably effective solution, creating strong, reliable connections with access required from only one side of the workpiece. Zoc Stud Weld stands as your partner in this technology, providing not just equipment but comprehensive support backed by deep manufacturing insight and a commitment to your project's success through our factory-direct approach and engineering prowess.
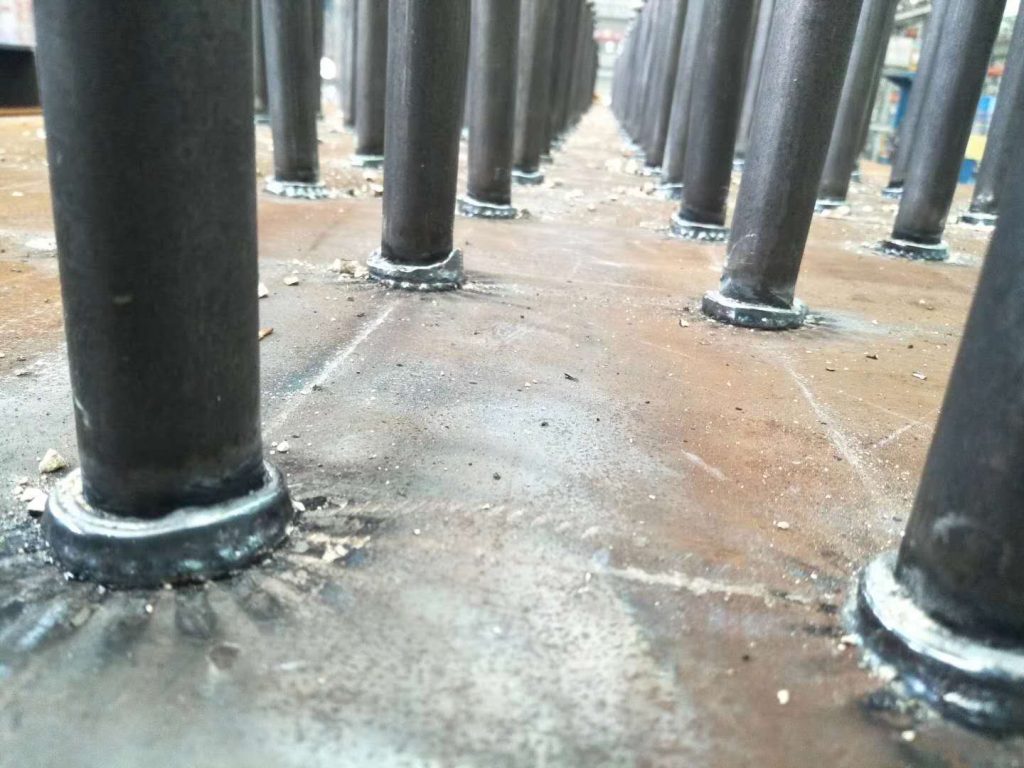
What Exactly Is Stud Welding and Why Is It Used?
Stud welding represents a specialized, high-speed arc welding process. It facilitates attachment of a metal stud, or a similar fastener, onto a metallic workpiece. This technique forges a high-quality metallurgical bond. You might be wondering: what makes this process so advantageous? Its primary appeal stems from creating an extremely strong, permanent fixture very rapidly. Often in mere seconds, or even fractions of a second, a stud becomes securely welded. This efficiency dramatically outpaces many conventional fastening methods like drilling and tapping, or manual nut-and-bolt assembly, especially across large-scale applications. The resulting weld joint typically possesses strength exceeding that of the stud or parent material itself, ensuring a durable and dependable connection under various operational stresses.
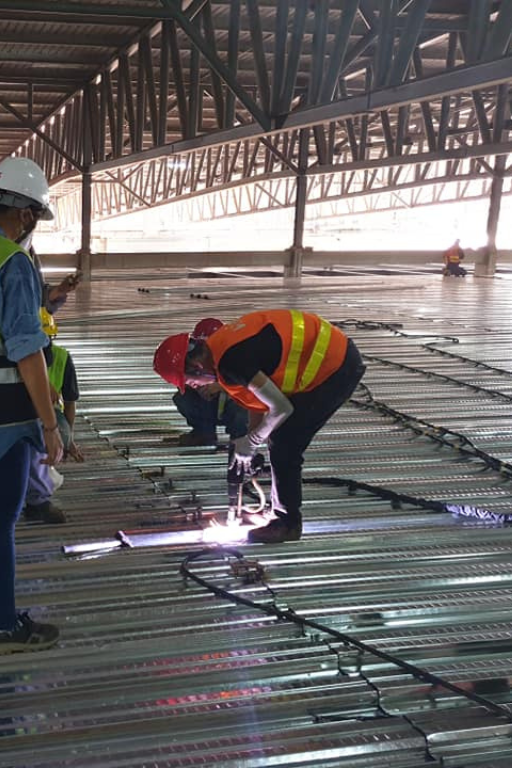
Furthermore, a significant benefit involves access. Stud welding uniquely requires access from only one side of the base material. This characteristic proves invaluable in situations where the reverse side is inaccessible or where maintaining a smooth, unmarred reverse surface is critical for aesthetic or functional reasons. Think about applications like attaching insulation pins inside ductwork, mounting components on sealed enclosures, or affixing wear studs to earthmoving equipment without compromising internal integrity. The process also minimizes distortion of the base material due to its very localized and rapid heat input, a crucial factor when working with thinner sheets or heat-sensitive components. This precision helps maintain the structural integrity and dimensional accuracy of the final assembly, a key consideration for quality-conscious engineering contractors and construction firms globally. Industries from shipbuilding and automotive manufacturing to power plant construction and bridge building extensively rely upon stud welding for its speed, reliability, and versatility in joining diverse metallic components. Its capacity to automate also lends itself well to high-volume production environments, further enhancing its appeal for modern industrial operations seeking productivity gains without sacrificing connection quality. Zoc Stud Weld provides a full spectrum of solutions, from shear studs and weld studs to ceramic ferrules and advanced stud welding machines, empowering businesses to harness these benefits effectively.
Defining stud welding technology
At its core, stud welding technology encompasses a suite of processes where a metal fastener, typically a stud, is joined to a metal workpiece by heating both parts with an electric arc. This arc melts a portion of the stud and a corresponding area on the workpiece, creating a molten pool. The stud is then plunged into this pool, and upon cooling, a solid, one-piece, full-strength weld forms. It's simpler than you think: the entire operation is usually automated within a stud gun, which controls the arc timing, lift (if applicable), and plunge. This controlled automation ensures consistent weld quality and high repeatability, which are paramount in demanding B2B applications. The technology is broadly categorized into two main methods: Drawn Arc (DA) stud welding and Capacitor Discharge (CD) stud welding, each suited for different stud diameters, base material thicknesses, and application requirements. DA welding typically handles larger diameter studs and often employs ceramic ferrules to shield and shape the weld, while CD welding is ideal for smaller diameter studs on thinner materials, offering a very quick weld with minimal heat affectation and often requiring no ferrule. Understanding this fundamental technology allows businesses to select the appropriate method and equipment for their specific fastening challenges, ultimately leading to more efficient and reliable product assemblies or construction projects.
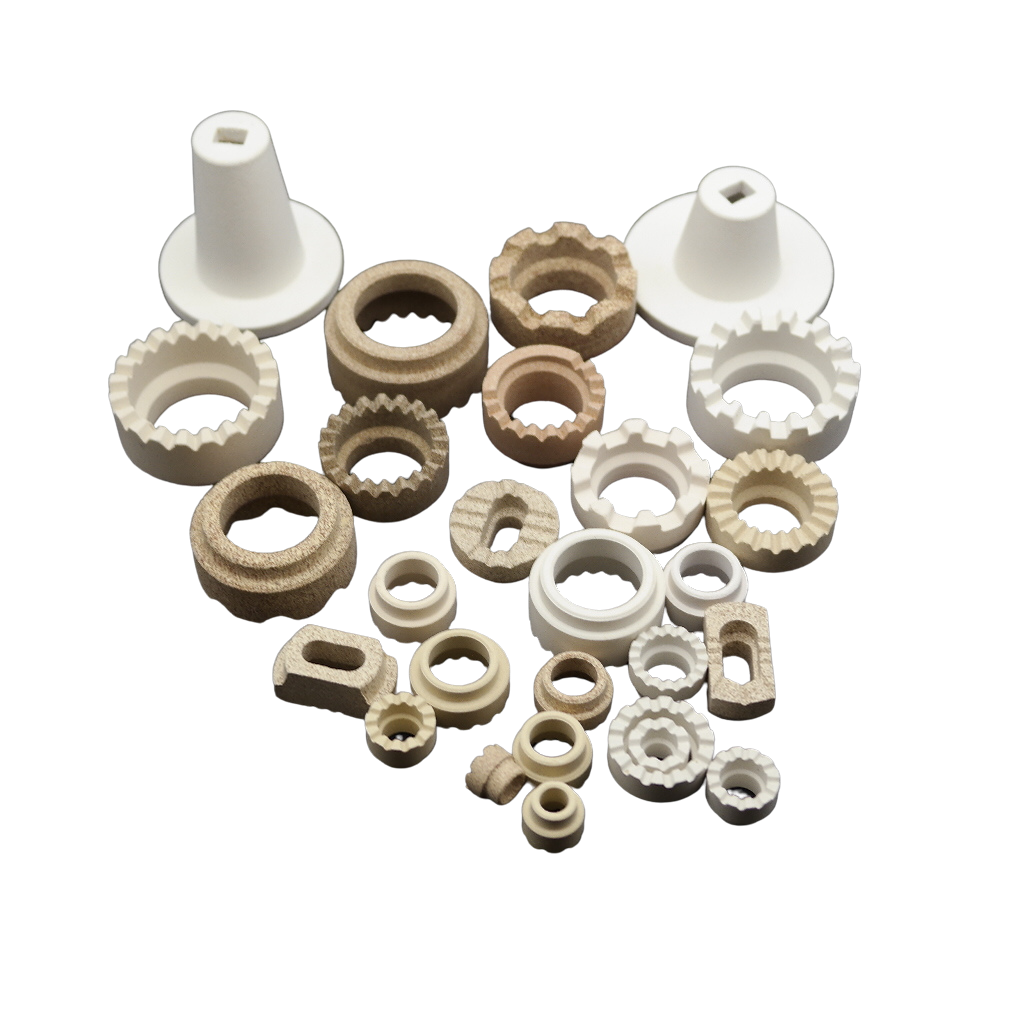
Key benefits in construction and manufacturing
The adoption of stud welding brings forth a multitude of key benefits particularly impactful within the construction and manufacturing sectors. Consider this: one primary advantage is the substantial increase in productivity. Welding a stud takes only a fraction of the time required for traditional methods like drilling, tapping, and then inserting and tightening a bolt. This speed translates directly into reduced labor costs and faster project completion times, a critical factor for international engineering contractors and construction firms managing tight deadlines. Another significant benefit is the superior strength of the weld. A properly executed stud weld creates a full cross-sectional bond, often stronger than the stud or the parent material itself. This robust connection enhances the structural integrity and durability of the final product or assembly. Furthermore, stud welding offers design flexibility. Since access is only needed from one side of the workpiece, designers are less constrained, and it allows for cleaner, more aesthetically pleasing designs as there are no protrusions or marks on the reverse side. This is particularly beneficial in applications where a smooth surface is required. The process also minimizes material distortion due to the rapid and localized heat input, preserving the integrity of the base material. The bottom line is: these benefits collectively contribute to higher quality products, reduced manufacturing costs, and improved operational efficiency for businesses across various industries.
Common industries relying on stud welding
Numerous industries heavily rely on stud welding technology due to its inherent advantages in creating strong, fast, and reliable fastenings. You see it everywhere: In the construction sector, it's fundamental for attaching shear connectors in composite steel construction (steel beams to concrete slabs in buildings and bridges), securing insulation, and fixing façade elements. The automotive industry utilizes stud welding for attaching grounding studs, mounting brackets, and various components to vehicle chassis and bodies, benefiting from the speed and one-sided access. Shipbuilding is another major user, employing stud welding for fixing insulation, cable hangers, and outfitting components throughout vessels, where robust connections are vital in harsh marine environments. Manufacturers of industrial equipment, such as boilers, pressure vessels, and heat exchangers, depend on stud welding for attaching internal components and external fixtures. Even in agriculture, for constructing farm buildings and attaching components to machinery, stud welding provides durable solutions. The power generation industry, including nuclear and conventional power plants, uses stud welding for various applications requiring high integrity and long-term reliability. Essentially, any industry that requires permanent, high-strength fastening of metallic components, especially where speed, one-sided access, or minimal material distortion are critical, finds significant value in adopting stud welding techniques. Zoc Stud Weld proudly serves these diverse industries with tailored solutions.
Comparison with traditional fastening methods
When compared with traditional fastening methods such as drilling and bolting, riveting, or manual welding of nuts, stud welding presents a compelling case for superiority in many B2B applications. Let's break it down: Traditional methods often involve multiple steps – drilling a hole, sometimes tapping threads, inserting a bolt or rivet, and then tightening or peening. Each step consumes time and labor. Stud welding, conversely, is a single, rapid operation. This speed advantage translates into significant labor cost savings and increased throughput. Strength-wise, a stud weld creates a full-fusion, homogenous joint, which is generally stronger and more fatigue-resistant than a mechanical fastener that relies on clamping force or shear resistance of the fastener body. Mechanical fasteners can also loosen over time due to vibration, a problem less prevalent with properly executed stud welds. Riveting, while offering one-sided access for some types, may not provide the same tensile strength as a stud weld, and the hole preparation can weaken the parent material. Manual welding of nuts or other attachments is slow, requires skilled labor, and can introduce more heat distortion than the controlled, localized heat of stud welding. The takeaway is clear: while traditional methods have their place, stud welding often provides a more efficient, stronger, and cleaner fastening solution, particularly for high-volume production or critical structural connections, making it a preferred choice for forward-thinking engineering and construction enterprises.
How Does the Drawn Arc Stud Welding Process Function?
The drawn arc stud welding process stands as a cornerstone for heavy-duty fastening applications, particularly favored in construction and heavy fabrication. So, how does it actually work? This method involves a precisely controlled sequence of events to create an exceptionally strong weld. It begins with the stud, loaded into a specialized weld gun, being pressed against the workpiece. A ceramic ferrule, crucial for this process, typically surrounds the weld end of the stud. This ferrule acts as a miniature mold, containing the molten metal, shaping the weld fillet, and shielding the arc from atmospheric contamination. The process is highly regarded for its ability to weld larger diameter studs, often ranging from 3mm up to 25mm or even larger, to relatively thick base materials, generally 2mm and above. Its robustness and the quality of the resulting weld make it indispensable for structural connections where integrity is paramount. Zoc Stud Weld offers a comprehensive range of drawn arc equipment and consumables, ensuring you have the right tools for these demanding tasks.
Explaining the drawn arc mechanism (lift, arc, plunge)
The magic of drawn arc stud welding unfolds in three distinct phases: lift, arc, and plunge. It all happens in a flash: First, when the operator triggers the weld gun, an initial low current, known as the pilot arc, is established. Simultaneously, the gun mechanism lifts the stud a predetermined distance away from the workpiece. This lift action draws out the pilot arc. Immediately following the lift, the main welding current, which is significantly higher, initiates. This powerful arc melts the end of the stud and a corresponding area on the base material, creating a pool of molten metal. The duration of this arc is precisely timed, typically lasting from a fraction of a second to just over a second, depending on the stud diameter and material. Finally, at the exact moment the arc extinguishes, the weld gun plunges the stud, under controlled spring pressure, into the molten pool on the workpiece. The molten metals solidify, forming a complete, full-fusion weld. The entire cycle is automated within the gun and power source, ensuring consistency and high weld quality. This precise control over each phase is what gives drawn arc stud welding its renowned strength and reliability.
Role of ceramic ferrules and flux
Ceramic ferrules play a vital, multifaceted role in the drawn arc stud welding process. Think of them as unsung heroes. These disposable ceramic rings, placed around the weld end of the stud before welding, serve several critical functions. Firstly, they help concentrate the arc heat, leading to more efficient melting of the stud and base material. Secondly, they act as a dam or mold to contain and shape the molten weld metal, forming a neat, uniform weld fillet around the base of the stud. This is particularly important for achieving consistent weld profiles and strength. Thirdly, the ferrule shields the molten weld pool from atmospheric oxygen and nitrogen, which could otherwise cause porosity and embrittlement in the weld. Some studs used in the drawn arc process also contain a small amount of flux, often in an aluminum ball or as a coating at the weld end. This flux vaporizes during the arc, providing additional deoxidizing and arc stabilizing effects, further enhancing weld quality by cleansing the weld area and promoting a smoother arc. After the weld cools, the ceramic ferrule is easily broken away and discarded, revealing the clean, strong weld beneath.
Typical applications and suitable materials
Drawn arc stud welding finds its place in a vast array of applications where robust and reliable fastening is non-negotiable. Its versatility is a key strength. In the construction industry, it's extensively used for attaching shear connectors to steel beams in composite bridge and building construction, securing concrete anchors, and fixing façade systems. Shipbuilding relies on it for attaching insulation, cable hangers, and various outfitting components. Heavy equipment manufacturing, including agricultural machinery, earthmoving equipment, and railcars, uses drawn arc studs for mounting components and wear parts. Power generation facilities, both conventional and nuclear, employ this method for critical connections. The process is well-suited for welding studs to mild steel, low-alloy steels, and stainless steels. While aluminum stud welding is possible with drawn arc using shielding gas instead of ferrules, it's a more specialized application. The ability to weld large diameter studs to relatively thick and sometimes imperfect surfaces makes it a go-to solution for many structural and heavy engineering projects. Zoc Stud Weld can provide expert advice on the suitability of drawn arc welding for your specific application and material combinations.
Advantages and limitations of drawn arc stud welding
Like any specialized process, drawn arc stud welding offers a distinct set of advantages alongside some limitations. Knowing these helps in making informed decisions. The primary advantages include the ability to weld large diameter studs (typically 3mm to 25mm+), creating very high-strength, full-penetration welds. It's suitable for thicker base materials (2mm and above) and can tolerate some surface imperfections or mill scale, thanks to the fluxing action and higher energy input. The use of ceramic ferrules ensures good weld profile and protection. However, there are limitations. The process generally requires a three-phase power supply due to the higher current demands. The use of ferrules means an additional consumable and a post-weld step to remove them. While it can handle some surface irregularities, very rusty or heavily contaminated surfaces still require cleaning. The heat input, though localized, is more significant than with Capacitor Discharge welding, which might be a concern for very thin or heat-sensitive materials. Also, the equipment tends to be larger and heavier than CD stud welding systems. Despite these limitations, for applications demanding maximum strength and reliability with larger studs, the advantages of drawn arc stud welding often outweigh the drawbacks, making it an indispensable technology for many industries.
Feature | Drawn Arc Stud Welding |
---|---|
Stud Diameter Range | Typically 3mm - 25mm+ |
Base Material Thickness | Generally 2mm and thicker |
Weld Strength | Very High, Full Penetration |
Power Requirement | Usually 3-Phase AC or DC |
Consumables | Studs, Ceramic Ferrules (Flux often in stud) |
Surface Condition | Tolerates some mill scale/rust |
Heat Affected Zone | Moderate |
Cycle Time | 0.1 to 1.5 seconds (approx.) |
Typical Use | Structural steel, heavy equipment, shipbuilding |
Reverse Side Marking | Generally none, but more heat input than CD |