What is Stud Welding? A Comprehensive Overview
Stud welding is a welding technique used to attach metal studs to a workpiece. This process is widely used in construction, manufacturing, and industrial applications to create strong, reliable bonds. The technique is highly regarded for its speed, precision, and ability to provide durable connections without the need for additional fasteners. In this article, we’ll explore what stud welding is, its various types, applications, and why it is considered one of the most efficient and reliable welding methods in modern industry.

1. What is Stud Welding and How Does It Work?
Stud welding is an efficient connection technology that attaches metal studs or other fasteners to the surface of workpieces through welding. First proposed by a British engineer in the 1930s, the technology has evolved over nearly a century and has become an indispensable process in modern manufacturing. The core advantage of this technology lies in its ability to quickly and reliably connect dissimilar materials (such as metal and concrete), while maintaining a smooth, blemish-free backside of the workpiece, making it especially suitable for thin sheet applications.
Technically, stud welding is mainly divided into two categories: capacitor discharge (energy storage) and drawn arc welding. Capacitor discharge stud welding utilizes the instantaneous high energy (around 1,600 Ws) generated by the discharge of a capacitor, completing the welding in a very short time (1-5 milliseconds). The depth of fusion is only about 0.1mm, with almost no deformation or indentation on the backside of the workpiece, making it ideal for welding thin sheets with thicknesses between 0.5-2mm. On the other hand, drawn arc stud welding uses a DC power source to generate a continuous arc, with a longer welding time (ranging from 20 to 2000 milliseconds), resulting in a larger depth of fusion and the ability to weld studs up to 30mm in diameter, providing higher connection strength.
From a process perspective, stud welding offers the following notable advantages:
- High efficiency and speed: Welding a stud takes only a few milliseconds to seconds. Manual welding speeds can reach up to 15 studs per minute, while automated equipment can achieve up to 50 studs per minute.
- Reliable connections: The welded joint has a high strength, with the stud's pull-out resistance typically no less than 5kN, meeting the structural connection requirements of most applications.
- Versatility: It can be used to weld a variety of materials, including carbon steel, stainless steel, aluminum, copper, and their alloys. The ratio of plate thickness to stud diameter can reach 1:10.
- Cost-effective and environmentally friendly: No need for drilling or tapping, reducing the consumption of auxiliary materials, lowering production costs, and saving energy.
With technological advancements, stud welding equipment has also been continuously upgraded and innovated. Modern welding systems commonly use microprocessor control and LCD displays, allowing precise setting and storage of welding parameters. They can also connect to computers via RS232 interfaces for data logging and quality traceability. The application of inverter technology has reduced the size of welding machines by 20%, decreased energy consumption by 30%, and increased welding speed by 100%, demonstrating the efficient and energy-saving development trend of stud welding technology.
2. What Are the Different Types of Stud Welding?
There are primarily three types of stud welding systems: drawn arc, capacitor discharge, and short-cycle stud welding. Each type offers unique advantages depending on the material being welded, the thickness of the workpiece, and the required welding speed.
Capacitor Discharge (CD) Stud Welding
- Process: Utilizes a capacitor to discharge electrical energy rapidly, creating a molten pool at the stud's tip. The stud is then pressed into the molten pool to form the weld.
- Applications: Ideal for thin materials (0.5–3 mm), such as sheet metal, HVAC systems, electrical enclosures, and signage. Commonly used in industries like automotive, electronics, and appliance manufacturing.
- Advantages:
- Minimal backside deformation.
- No need for shielding gas or ceramic ferrules.
- Fast welding cycle, typically under 1 millisecond.
- Suitable for small-diameter studs (M3–M12).
- Limitations:
- Not suitable for thick materials.
- Limited to specific stud types with pre-designed tips.
Drawn Arc (DA) Stud Welding
- Process: An electric arc is drawn between the stud and base material, melting both to form a weld. A ceramic ferrule is used to contain the molten pool and shape the weld.
- Applications: Used for structural applications requiring strong welds, such as steel construction, shipbuilding, and heavy equipment manufacturing.
- Advantages:
- Produces strong, durable welds.
- Suitable for a wide range of stud sizes (up to M30).
- Can weld to thick materials (≥2 mm).
- Limitations:
- Requires shielding gas or ceramic ferrules.
- Longer welding cycle compared to CD.
- Potential for backside spatter or deformation.
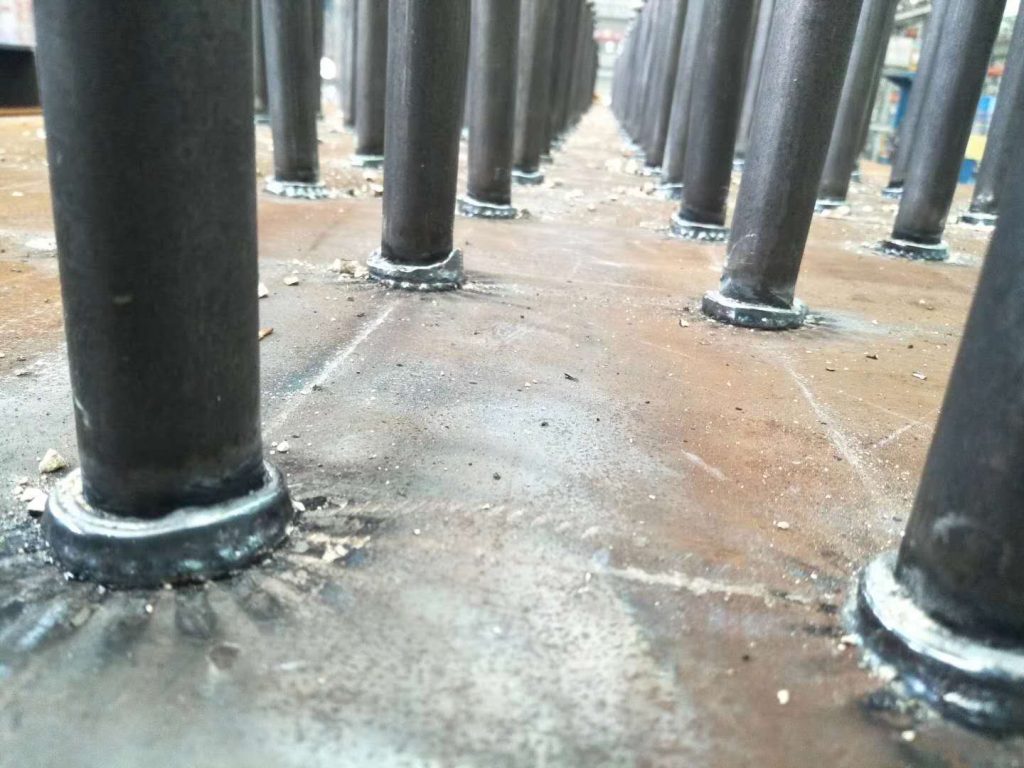
Short Cycle (SC) Stud Welding
- Process: A variation of drawn arc welding with shorter welding times (typically 20–100 milliseconds) and higher currents
- Applications: Suitable for thin materials (0.5–2 mm) and applications requiring faster welding speeds, such as automotive manufacturing and HVAC systems.
- Advantages:
- Faster welding cycle than standard DA.
- Reduced backside deformation compared to DA.
- No need for shielding gas or ceramic ferrules in some cases.
- Limitations:
- Not suitable for thick materials.
- May require specific stud types with flanges.
Comparison Table
Feature | Capacitor Discharge (CD) | Drawn Arc (DA) | Short Cycle (SC) |
---|---|---|---|
Welding Time | <1 ms | 20–100 ms | 20–100 ms |
Suitable Material Thickness | 0.5–3 mm | ≥2 mm | 0.5–2 mm |
Shielding Gas Required | No | Yes | Optional |
Ceramic Ferrule Required | No | Yes | Optional |
Suitable Stud Sizes | M3–M12 | M3–M30 | M3–M16 |
Applications | Sheet metal, signage | Structural steel, shipbuilding | Automotive, HVAC |
3. How is Stud Welding Applied in Construction?
Stud welding is an advanced metal fastening technique that plays a crucial role in a variety of industries, including construction, mining, automotive manufacturing, shipbuilding, electrical equipment, and home appliances. This technology provides efficient, reliable, and strong connections, helping improve structural integrity and reduce production costs.
Construction Industry
Stud welding has become indispensable in modern construction, particularly for steel and concrete composite structures. It efficiently connects metal and concrete materials, which traditionally had bonding issues due to different material properties.
- Shear Connectors in Steel-Concrete Composite Structures:
In composite floor systems, headed studs (shear connectors) are used to connect steel beams to reinforced concrete slabs. This method significantly increases the rigidity and load-bearing capacity of the floor. For example, in large-scale projects in Beijing, steel structures and lightweight steel partition walls are connected using stud welding, improving both time efficiency and material usage. In one particular project, the stud welding process saved 21 days of construction time and reduced costs by approximately 243,000 yuan. - Thermal Insulation Fixation:
Stud welding is used to secure thermal insulation materials like rock wool and glass wool to the exterior walls and roofs of buildings. This method avoids drilling holes and using adhesives, offering a faster and more environmentally friendly solution. Specialized stud welding machines like the CDi1502 are designed for this application, welding insulation pins at a rate of 14-40 pins per minute without burning through thin panels. - Decorative Component Installation:
Stud welding provides a hidden and strong connection method for installing components like glass curtain wall frames, metal decorative strips, and signage. This technique ensures the integrity of decorative surfaces, avoiding risks of water leakage and corrosion, especially in high-rise buildings. - Underground and Tunnel Engineering:
In subway stations, underground parking lots, and other underground structures, stud welding is used to connect waterproof steel plates to concrete or to fix various pipe and bracket systems. The process reduces construction time by up to 60% compared to traditional welding, and its lack of open flame operations makes it safer.
Mining and Heavy Equipment Applications
In mining and heavy machinery, stud welding plays a key role in enhancing wear resistance and extending the lifespan of equipment working in harsh environments. This technology has been used to protect machinery from abrasion, corrosion, and high-impact stresses.
- Excavator Bucket Reinforcement:
In mining, excavator buckets endure severe wear and tear from handling rocks and soil. By welding hard alloy composite studs to the bucket edges and bottom, the lifespan of the bucket can be extended by 3 to 5 times, significantly reducing maintenance costs. - Crusher and Milling Equipment Protection:
Stud welding technology is applied to attach wear-resistant studs to parts of crushers like jaw plates and hammerheads, which experience rapid abrasion. The hard tungsten carbide studs increase the resistance to material impact, reducing downtime for part replacements. - Conveyor System Wear Protection:
For conveyors in mines, stud welding is used to attach wear-resistant studs to the interior surfaces of chutes, hoppers, and bins, improving their durability and reducing maintenance intervals from 3 months to 18 months. - Drilling Equipment Enhancement:
In drilling rigs, special studs are welded to drill rods and bits, enhancing their wear resistance while helping control material flow. In the petroleum industry, this technology increases the lifespan of drill bits by over 30%.
Automotive Manufacturing
Stud welding is a critical process in automotive manufacturing, replacing traditional riveting, threading, and drilling. It is used to secure components in car bodies and subassemblies, offering increased production efficiency and consistent quality.
- Vehicle Body Assembly:
In car body assembly, stud welding is used to attach hundreds of different studs to secure components like wiring harnesses, fuel lines, heat shields, and interior decorations. For instance, the Citroën C5 model uses 187 studs, demonstrating the extensive use of stud welding in modern automotive production lines. - Interior Systems:
In automotive interiors, components like headliners, carpet fittings, and interior panels are welded using stud welding. This method is much faster than traditional screw fastening, with some models able to complete 40 welds per minute, significantly reducing production time. - Chassis and Suspension Parts:
For chassis components, stud welding uses corrosion-resistant stainless steel studs to avoid the corrosion problems that can arise from drilling holes in metal parts. - Safety System Installations:
Safety-critical components such as airbag modules and sensors are secured using stud welding, providing reliable and durable connections that meet stringent safety standards.
Shipbuilding and Marine Engineering
Stud welding plays a vital role in shipbuilding and marine engineering, where it is used for installing structural and decorative components in harsh marine environments.
- Deck Equipment Installation:
Ship deck equipment like railings, mooring devices, and hatch covers are securely fastened using stainless steel or galvanized studs. This method ensures strong and flexible connections, reducing deformation and simplifying maintenance. - Interior Systems:
In ship interiors, stud welding is used for attaching partition walls, ceilings, and furniture, ensuring a clean appearance without visible fasteners. In luxury cruise ships, stud welding is applied to over 20,000 studs, saving 30% of installation time compared to traditional methods. - Marine Pipe Supports:
Stud welding is also used to attach studs to ship hulls for supporting pipes, reducing installation time and enhancing flexibility for future maintenance and upgrades.
Electrical Equipment and Home Appliances
Stud welding provides a precision fastening solution for both large electrical switchgear and small household appliances.
- Home Appliances:
In the production of home appliances like refrigerators and microwaves, stud welding is used to attach studs for securing various components, ensuring both strength and aesthetic quality without visible fasteners. - Electrical Switchgear:
In the manufacture of high and low-voltage switchgear, stud welding is used to secure internal components and panels. It ensures minimal heat input and prevents damage to the metal surface while providing strong and reliable connections. - Control Panels and Transformer Housing:
For transformer housings and control panels, studs are welded onto the sheet metal to ensure a stable and long-lasting assembly. The ability to weld without causing deformation or damage to thin panels makes stud welding particularly useful in these applications.
4. What Are the Advantages of Stud Welding Over Other Welding Techniques?
Stud welding offers several distinct advantages compared to traditional welding techniques, such as MIG or TIG welding. The primary benefits include speed, precision, and the ability to weld without filler materials. This makes stud welding ideal for high-volume production environments where time and cost are critical factors.
One of the most significant advantages of stud welding is the reduced need for post-weld finishing. Since the welds are created in one quick, clean process, the need for additional smoothing or cleanup is minimal. This contributes to the overall efficiency of the process, saving both time and labor costs.
Moreover, stud welding creates highly reliable connections, which are particularly important in industries like aerospace, automotive, and heavy machinery. These industries require welds that can withstand extreme conditions, such as high stress and exposure to corrosive elements.
Advantages of Stud Welding Compared to Other Techniques
Advantage | Stud Welding | MIG Welding | TIG Welding |
---|---|---|---|
Speed | Very fast | Moderate | Slow |
Precision | High | Moderate | Very high |
Post-weld Cleanup | Minimal | Requires cleaning | Requires cleaning |
Equipment Cost | Moderate | High | Very high |
5. How Do Stud Welding Machines Work?
Stud welding machines operate by rapidly fusing metal studs to the surface of a workpiece through an electric arc, which involves key stages such as energy conversion, metal melting, and rapid solidification. Here's a detailed technical breakdown of how stud welding machines work:
Core Working Principle
Energy Conversion System
- Capacitor Discharge Welding Machine:
Capacitor banks store electrical energy (typically 1600Ws) and release peak currents of up to 5000A in 1-5 milliseconds when discharged. - Drawn Arc Welding Machine:
Inverters convert AC power to DC (400-2000A) for durations of 20-2000 milliseconds. - Modern welding machines achieve energy efficiency of up to 85%, saving 30% more energy compared to traditional welding methods.
Arc Formation Mechanism
- Short-Cycle Drawn Arc Welding:
The stud is lifted by 1.0-1.5mm to form an arc, reaching temperatures between 8000-15000°C. - Capacitor Discharge Welding:
There is no lifting; instead, an arc is generated directly through the stud's tip, creating a plasma channel for welding.
Working Process (Using Drawn Arc Welding as an Example)
Positioning Stage
- The welding gun applies vertical pressure to the stud, with a pressure sensor detecting contact pressure (typically 20-50N).
Arc Ignition Stage
- When powered, the welding gun lifts the stud by 1.2±0.2mm to form a stable arc (voltage between 18-32V).
Melting Stage
- Both the base material and the stud tip melt simultaneously, forming a molten pool with a diameter approximately 1.3 times that of the stud (e.g., M8 stud forming a ~Φ10.4mm molten pool).
Immersion Stage
- The welding gun's cylinder pushes the stud into the molten pool at a speed of 0.8-1.2m/s to ensure the proper mixing of molten metals.
Solidification Stage
- After power is cut off, the molten pool solidifies rapidly under pressure, cooling at rates of up to 10^4-10^6 K/s, forming a fine-grained structure.
Key Subsystems
Subsystem | Capacitor Discharge Welding Machine | Drawn Arc Welding Machine |
---|---|---|
Power System | Capacitor energy storage (e.g., CD99 model, 99000μF) | Inverter/Thyristor rectifier (e.g., RSN-3150HD) |
Control System | Microcontroller-based intelligent control (touchscreen settings) | PLC/Microcontroller control (adjustable current, time) |
Welding Gun System | Contact-type (C08) or lift-type (CA08) | Pneumatic/servo-motor-driven (high-precision lift) |
Cooling System | Natural or air cooling | Temperature-controlled air cooling (prevents overheating) |
Monitoring System | Voltage detection module | Real-time current/voltage waveform acquisition (10kHz) |
Key Parameters
Capacitor Discharge Welding Machine
Parameter | Typical Range | Effect |
---|---|---|
Discharge Time | 1-3ms | Shorter time, smaller heat-affected zone |
Charging Voltage | 25-200V DC | Higher voltage, more welding energy |
Stud Diameter | 2-10mm | Suitable for low-carbon steel, stainless steel, aluminum |
Welding Speed | 40 parts/min (automatic) | Dependent on capacitor charging speed |
Drawn Arc Welding Machine
Parameter | Typical Range | Effect |
---|---|---|
Welding Current | 300-2000A | Every 100A increase adds 0.2mm to penetration depth |
Welding Time | 20-2000ms | Every 1ms increase raises molten pool temperature by 15°C |
Lift Height | 1.0-2.5mm | Affects arc stability |
Protection Method | Ceramic Ring/Gas Protection | Prevents oxidation, improves weld seam formation |
Domestic Typical Applications
- Construction Industry: Steel-concrete shear connections (e.g., φ19mm stud, 1800A, 1.2s welding time).
- Automotive Manufacturing: Short-cycle drawn arc welding (M6 studs, 600A, 30ms, 40 parts/min).
- Home Appliance Industry: Capacitor discharge welding for securing insulation pins (M3-M8, 14-40 parts/min).
Common Issues and Solutions
- Arc Deflection: Optimize the grounding clamp position and avoid sharing the ground with other welding machines.
- Weld Failure: 80% of the time, it is due to incorrect welding gun parameters (pressure/lift height); adjustments per the manual should resolve this.
- Porosity/Cracking: Use argon gas protection (flow rate 8-12L/min) or preheat to 80-120°C (for high-carbon steels).
6. How Do You Select the Right Stud Welder for Your Project?
Choosing the right stud welder for your project is crucial to achieving optimal results. Selecting a stud welder involves considering factors such as the material to be welded, the thickness of the workpiece, and the required speed and precision. Each type of stud welding machine is designed to handle specific tasks, so understanding the application is key.
For example, if you are working with thin materials, a capacitor discharge stud welder may be the best choice. These machines provide rapid, precise welding with minimal heat input, making them ideal for delicate applications. On the other hand, if you need to weld thicker materials, a drawn arc welder would be more appropriate, as it delivers higher power and is better suited for heavy-duty tasks.
Additionally, the size of the job and production speed requirements play a role in determining the ideal stud welder. For large-scale projects, a machine that can handle high volumes of welds in a short amount of time will be necessary. A quality stud welder should also offer adjustable power settings and be compatible with various stud sizes for maximum flexibility.
Choosing the Right Stud Welder
Criteria | Capacitor Discharge Welder | Drawn Arc Welder | Short-Cycle Welder |
---|---|---|---|
Material Type | Thin materials | Thick materials | Medium materials |
Power Requirements | Low | High | Moderate |
Speed | Fast | Moderate | Moderate |
Ideal Applications | Automotive, light fabrication | Heavy construction | Precision welding |
Adjustability | High | Low | Moderate |
7. What Are the Common Issues in Stud Welding and How Can They Be Avoided?
Like any welding technique, stud welding can experience issues that affect the quality of the weld. Common problems include porosity, undercut, and incomplete fusion. These issues can often be traced back to improper heat settings, incorrect stud positioning, or poor-quality materials. Let’s break down how to avoid these common pitfalls.
First, porosity occurs when gas bubbles get trapped in the weld, leading to weak spots. This is often caused by contaminated materials or improper welding techniques. To prevent this, ensure that the workpiece and stud are clean and free from oils, rust, or other contaminants.
Undercut refers to the thinning of the base metal at the edge of the weld, which can result in reduced strength. This problem is usually caused by excessive heat. To avoid undercut, use the correct power settings and ensure that the welding time is properly controlled.
Finally, incomplete fusion can occur when the stud and workpiece don’t fuse properly, often due to insufficient heat or incorrect placement of the stud. Ensure that the stud is properly aligned and that the heat is applied evenly for consistent bonding.
Common Issues in Stud Welding and How to Avoid Them
Issue | Cause | Prevention |
---|---|---|
Porosity | Contaminants, improper heat | Clean materials, proper heat settings |
Undercut | Excessive heat | Adjust power, control welding time |
Incomplete Fusion | Improper stud placement, low heat | Align stud correctly, use adequate heat |
8. How Does Stud Welding Compare to Other Joining Techniques?
Stud welding offers several advantages over traditional joining techniques such as bolting, riveting, and other welding methods. Compared to bolting, stud welding is faster and provides a more secure bond. Bolted joints require additional steps, such as drilling holes and fastening, while stud welding creates a solid bond in a single step, reducing both labor and time.
Riveting, another common method, involves physically deforming the material to create a secure connection. However, rivets can loosen over time due to vibrations, making them less reliable than welds. Stud welding provides a permanent, non-mechanical connection that is far more durable.
When compared to traditional welding methods like MIG or TIG, stud welding is often quicker and more cost-effective, especially in high-volume production. It doesn’t require the use of filler materials, which reduces costs and waste.
Comparison of Stud Welding to Other Joining Techniques
Method | Speed | Strength | Cost | Applications |
---|---|---|---|---|
Stud Welding | Very fast | Very high | Moderate | Automotive, construction |
Bolting | Moderate | High | Low | Structural connections |
Riveting | Moderate | Moderate | Low | Aircraft, heavy machinery |
MIG/TIG Welding | Moderate | Very high | High | General fabrication |
9. What Are the Safety Considerations in Stud Welding?
Safety is paramount when performing stud welding, as the process involves high temperatures and electricity. Understanding the potential hazards and taking the necessary precautions can help prevent accidents. First, always wear the appropriate personal protective equipment (PPE), including gloves, goggles, and flame-resistant clothing.
Additionally, the work area should be free of flammable materials, as the welding process generates intense heat. Electrical safety is also crucial, so ensure that machines are properly grounded and that all wiring is secure and undamaged.
To further minimize risk, operators should be trained in the safe handling of stud welding equipment. Regular maintenance of the equipment and proper storage of welding materials will help ensure safe operation over time.
Safety Measures for Stud Welding
Safety Measure | Purpose |
---|---|
Personal Protective Equipment | Protects against burns, sparks |
Proper Grounding of Machines | Prevents electrical hazards |
Clear Work Area | Reduces risk of fire or explosion |
Equipment Maintenance | Ensures safe operation |
10. How Can Stud Welding Impact Product Quality and Durability?
The impact of stud welding on product quality and durability is significant. Stud welding provides strong, reliable connections that can withstand high levels of stress and strain. This makes it an ideal choice for industries such as aerospace, automotive, and heavy machinery, where product reliability is critical.
Moreover, the quick and precise nature of stud welding ensures minimal heat distortion, which helps preserve the integrity of the surrounding materials. Unlike other methods that may cause warping or deformation, stud welding creates a clean, secure bond that enhances the overall durability of the product.
In terms of long-term performance, stud welding provides a strong bond that resists corrosion and wear. This means that products welded using stud welding are more likely to perform well over time, even in harsh environments.
Impact of Stud Welding on Product Quality
Impact | Benefit | Example Applications |
---|---|---|
Strength | High tensile strength | Automotive, aerospace |
Durability | Resistance to wear and corrosion | Heavy machinery, construction |
Precision | Minimal heat distortion | Precision parts, aerospace |
11. What Maintenance is Required for Stud Welding Machines?
Maintaining your stud welding machine is crucial for ensuring consistent performance and long-lasting durability. Regular maintenance tasks include cleaning the welding gun, checking the power supply for wear, and ensuring that the stud holder is functioning correctly.
Additionally, it’s important to calibrate the machine regularly to ensure that the welding power and speed are set correctly for the job. Regular inspection of the electrical components is also necessary to prevent short circuits and power failures.
Scheduled maintenance can prevent unexpected breakdowns and extend the lifespan of your equipment, ensuring that it remains reliable even after years of heavy use.
Maintenance Tasks for Stud Welding Machines
Task | Frequency | Purpose |
---|---|---|
Clean welding gun | Weekly | Prevents build-up and ensures smooth operation |
Check power supply components | Monthly | Ensures consistent power output |
Calibrate machine | Quarterly | Maintains proper settings for optimal performance |
12. How Do You Troubleshoot Stud Welding Machines?
When a stud welding machine encounters an issue, it’s important to quickly diagnose and resolve the problem to avoid downtime. Common issues include inconsistent welds, power failure, and poor stud positioning. Here’s how to troubleshoot these issues.
Inconsistent welds may be caused by improper heat settings or dirty materials. To fix this, check the power settings and ensure that both the stud and workpiece are free of contaminants. Power failure is often due to an electrical issue, so inspect the wiring and connections. Finally, if the studs are not aligning properly, check the stud holder and ensure it’s properly positioned.
Common Troubleshooting Solutions
Problem | Cause | Solution |
---|---|---|
Inconsistent welds | Incorrect heat settings | Adjust power settings |
Power failure | Electrical issue | Inspect wiring and connections |
Poor stud alignment | Misaligned stud holder | Adjust holder position |
13. What Future Trends Are Emerging in Stud Welding Technology?
As technology continues to advance, the stud welding industry is seeing innovations that enhance efficiency, precision, and sustainability. Automation and artificial intelligence (AI) are playing a significant role in improving the speed and accuracy of stud welding processes. Automated systems can now handle more complex tasks, reducing human error and improving overall production quality.
Moreover, sustainable practices are becoming increasingly important in manufacturing, and stud welding is no exception. New developments in energy-efficient machines and eco-friendly materials are making the process more sustainable. These innovations ensure that stud welding remains a reliable, cost-effective solution for businesses while also minimizing environmental impact.
Future Trends in Stud Welding Technology
Trend | Impact on Industry | Example |
---|---|---|
Automation | Increased speed, precision | Automated stud welding systems |
Sustainability | Reduced environmental impact | Eco-friendly welding materials |
Conclusion
In conclusion, stud welding is an efficient, reliable, and cost-effective solution for joining metal studs to a workpiece. Its speed, precision, and versatility make it an essential technique in industries such as construction, automotive, and aerospace. By choosing the appropriate stud welding method, businesses can ensure strong, durable connections that meet industry standards.
Backed by years of experience and innovation, companies like ZOC Industrial have built a reputation for offering top-quality stud welding equipment and unparalleled customer support. Our equipment is engineered to meet the rigorous demands of various industries, ensuring that your projects are completed on time, within budget, and to the highest standards. Trust us to be your partner in success, delivering reliable and efficient stud welding solutions for all your needs.
FAQ Section
Q1: What is stud welding?
Stud welding is a process that attaches a metal stud to a workpiece using heat and pressure. It is commonly used in construction and industrial applications to create strong, durable welds.
Q2: How does stud welding work?
Stud welding works by generating an electric arc to melt the base of the stud and the surface of the workpiece. The stud is then pressed onto the molten surface, creating a bond as it cools.
Q3: What are the advantages of stud welding over other welding techniques?
Stud welding is faster and more efficient than traditional welding methods. It also requires less post-weld cleanup and creates highly reliable, strong connections, making it ideal for high-volume production.
Q4: What materials can be welded using stud welding?
Stud welding can be performed on materials such as steel, stainless steel, and aluminum. Each material requires different levels of heat and precision during the welding process.
Q5: How do I select the right stud welder for my project?
When selecting a stud welder, consider factors like the material to be welded, the thickness of the workpiece, and the required speed. A high-quality welder should also offer adjustable power settings for different applications.