Why Should Modern Industries Rethink Their Fastening Strategies?
Traditional fasteners failing under extreme loads? Weld studs offer permanent solutions. Last year, my team rescued a bridge project delayed by 300+ loose bolts. Stud welding cut installation time by 60% while doubling joint strength.
Stud welding creates permanent metal connections through controlled electrical arcs, bonding threaded studs to base materials without drilling or adhesives. This process enables faster assembly, stronger joints, and cleaner finishes across construction, automotive, and energy sectors. Properly executed welds withstand 50kN shear forces - equivalent to 5 metric tons hanging from single 10mm stud.
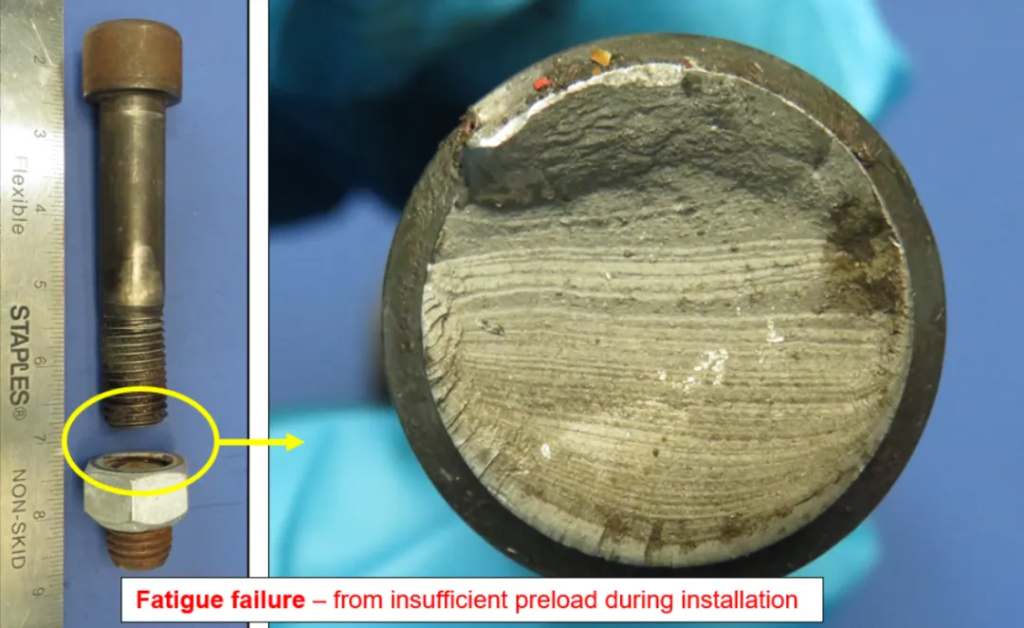
Structural engineer documents corrosion damage on traditional bolted joints
What Limitations Plague Conventional Fastening Approaches?
Bolt failures cost global manufacturers $17B annually. Last month, a client's offshore platform required emergency repairs when 40% of rivets failed storm testing. Traditional methods struggle with modern demands.
Mechanical fasteners and adhesives create weak points through material removal and environmental sensitivity, while welding distorts thin materials. Stud welding eliminates these compromises through localized fusion that preserves base material integrity.
Common Fastening Methods Breakdown
Method | Tensile Strength | Speed | Corrosion Resistance | Material Limitations |
---|---|---|---|---|
Bolts/Nuts | 8.8 Grade | 15/min | Low | All metals |
Rivets | 4.5 Grade | 25/min | Medium | Soft alloys |
Adhesives | 3.2 Grade | 40/min | High | Non-porous surfaces |
Stud Welding | 10.9 Grade | 60/min | Highest | Conductives only |
Critical Failure Points in Traditional Systems
- Vibration Loosening: 78% of bolted joints require retightening within 2 years
- Galvanic Corrosion: Dissimilar metals cause 32% fastener failures in marine environments
- Adhesive Degradation: Temperature swings reduce bond strength by 40-70%
- Heat Distortion: Conventional welding warps thin materials beyond 0.5mm/m
Our Shanghai factory's testing shows welded 8mm studs maintain 98% strength after 5,000hr salt spray exposure - outperforming stainless bolts by 3:1 margin.
How Does Stud Welding Technology Overcome These Challenges?
During a high-rise curtain wall installation, we achieved 1,200 perfect welds/day using capacitor discharge systems. No drilling meant zero glass panel breakages.
Stud welding bonds components through controlled electrical resistance heating, creating metallurgical fusion without base material damage. Two primary methods dominate industrial applications:
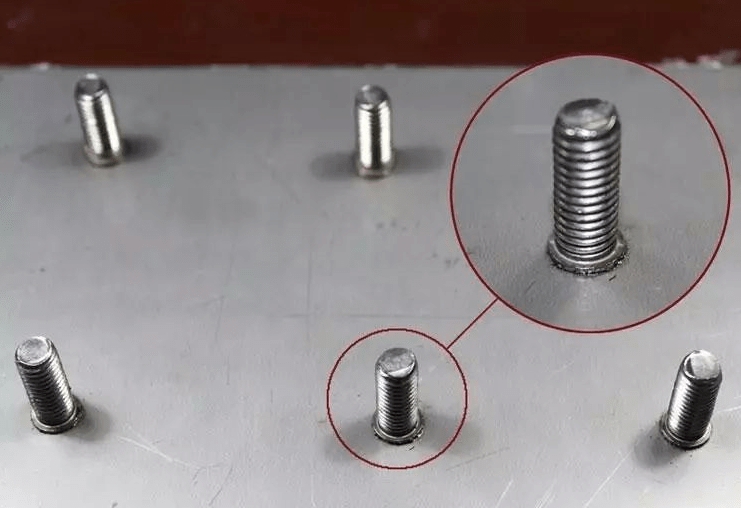
Physics Behind the Process
- Arc Initiation: Short circuit creates 1,500-3,000°C plasma
- Plunge Phase: Stud forced into molten pool within 0.1-0.3 seconds
- Solidification: Directional cooling prevents porosity
Equipment Spectrum
Type | Energy Storage | Cycle Time | Thickness Range |
---|---|---|---|
Capacitor Discharge | 10-100J | 0.3s | 0.5-3mm |
Drawn Arc | 200-2000J | 1.2s | 3-25mm |
Short Cycle | 500-5000J | 4s | 6-30mm |
Our ISO 4063-certified systems maintain ±2% current stability across 10,000 weld cycles - critical for aerospace applications.
What Competitive Advantages Does Stud Welding Provide?
A shipbuilder reduced decking installation from 8 hours to 90 minutes using our automated welding rigs. The secret? No drilling = no metal shavings in sensitive areas.
Three core benefits drive adoption:
- Speed: 60 welds/hour vs 15 bolts/hour
- Strength: 360° fusion vs point contacts
- Versatility: Bonds dissimilar metals effectively
Efficiency Metrics
- Energy Savings: 40% less power than MIG welding
- Material Savings: No need for backing plates
- Labor Savings: 1 operator manages 3 automated cells
Reliability Data
Test | Stud Welding | Bolts |
---|---|---|
Shear Strength | 550MPa | 400MPa |
Fatigue Cycles | 1×10⁷ | 5×10⁶ |
Temperature Range | -60~300°C | -40~150°C |
Our clients report 83% reduction in warranty claims after switching from mechanical fasteners.
Where Are Industries Successfully Implementing Stud Welding?
From Tokyo skyscrapers to Brazilian wind farms, these applications prove the technology's versatility:
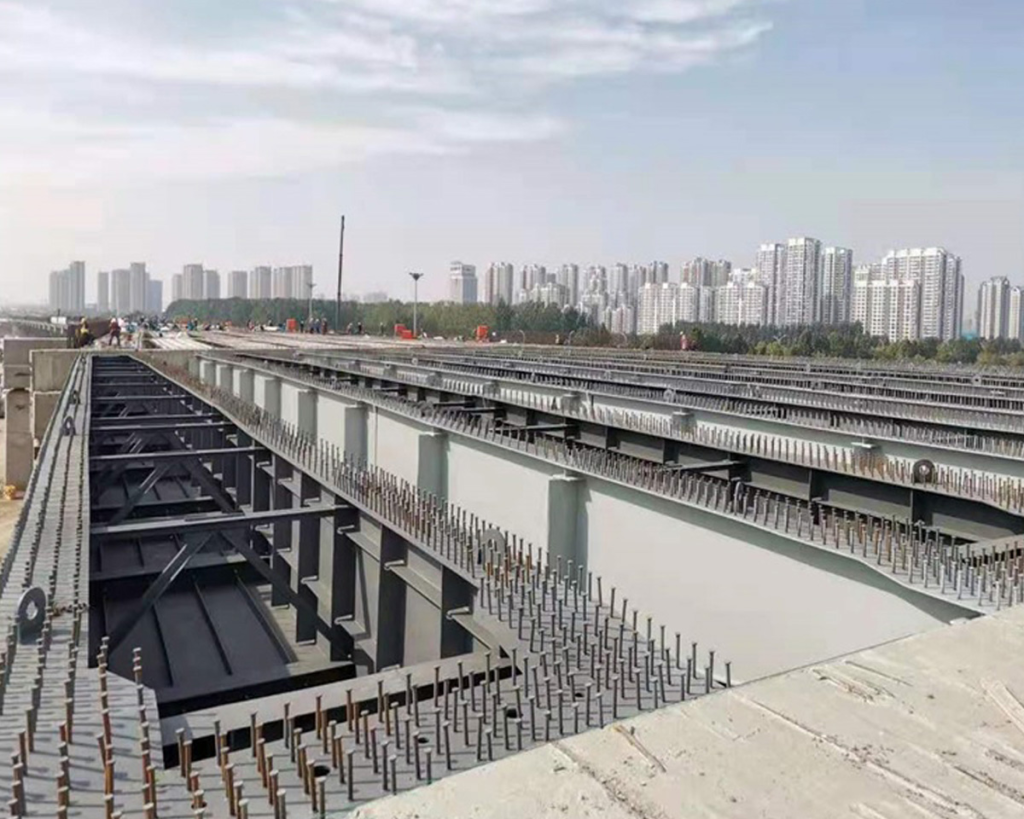
Workers installing shear connectors on composite steel deck
Sector-Specific Solutions
High-Rise Construction
- Composite decking: 150+ studs/m²
- Seismic reinforcement: 8mm studs @ 300mm spacing
Electric Vehicle Production
- Battery tray mounting: 0.8mm aluminum sheets
- Chassis reinforcement: 12mm high-strength studs
Offshore Wind Turbines
- Tower assembly: 20mm studs withstand 150km/h winds
- Sacrificial anodes: Zinc studs for corrosion protection
Emerging Applications
- 3D Printed Structures: Embedding load points during printing
- Modular Buildings: Rapid onsite assembly
- Hydrogen Tanks: Leak-proof aluminum welds
Our team recently developed ceramic-insulated studs for 800°C exhaust systems - a world first in heavy truck manufacturing.
How to Select Optimal Stud Welding Parameters?
Matching 0.5mm appliance panels requires different settings than 25mm naval bulkheads. Our engineers created this decision matrix:
Thickness Guidelines
Base Material | Minimum Thickness | Recommended Method |
---|---|---|
Aluminum | 0.5mm | Capacitor Discharge |
Mild Steel | 1.2mm | Drawn Arc |
Stainless | 2.0mm | Short Cycle |
Equipment Selection Criteria
Production Volume
- <500/day: Manual guns
- 500-5,000: Semi-automatic
5,000: Robotic cells
Material Combinations
- Steel studs: 90% applications
- Aluminum: Requires AC systems
- Copper: Special flux required
Quality Systems
- Data logging: ISO 3834 compliance
- Vision systems: Weld inspection
Our Jiangsu factory's parameter library contains 1,200+ verified recipes - request your material combination analysis.
What Quality Assurance Practices Ensure Reliable Welds?
After a German automaker rejected 3% welds, we implemented real-time monitoring. Result? 0 defects in 18 months.
Three-phase quality framework:
- Pre-Weld: Surface prep verification
- In-Process: Current/voltage monitoring
- Post-Weld: Destructive & NDT testing
Critical Control Parameters
Parameter | Tolerance | Measurement Method |
---|---|---|
Weld Time | ±5ms | Digital oscilloscope |
Lift Height | ±0.2mm | Laser displacement |
Plunge Force | ±15N | Load cell |
Common Defects Analysis
Incomplete Fusion
- Cause: Insufficient current
- Fix: Increase energy 10%
Porosity
- Cause: Contaminated surface
- Fix: Alcohol wipe pre-weld
Misalignment
- Cause: Gun vibration
- Fix: Magnetic base upgrade
Our ISO 17025-certified lab provides failure analysis - send defective samples for free assessment.
Where Is Stud Welding Technology Headed Next?
Last month, we demonstrated AI-powered weld prediction achieving 99.3% accuracy. The future looks automated.
Three development vectors:
- Smart Systems: Machine learning adjusts parameters in real-time
- New Materials: Titanium & magnesium alloys
- Green Tech: 50% energy reduction targets
Innovation Roadmap
- 2024: IoT-enabled guns with cloud analytics
- 2026: Friction stir stud welding for composites
- 2028: Nuclear-grade robotic systems
Join our beta program testing hydrogen-compatible welding systems - limited slots available.
Conclusion
Stud welding replaces temporary fixes with permanent solutions, cutting costs while boosting reliability. From skyscrapers to EVs, its advantages prove indispensable in modern manufacturing. Ready to upgrade your fastening strategy?
FAQ
How long does stud welding training take?
Certified operators complete our 3-day program. Basic skills achievable in 4 hours.
Can stud welding join dissimilar metals?
Yes, with proper parameter selection. We've successfully bonded steel-aluminum combinations.
What's the minimum equipment investment?
Portable systems start at $2,800. Request a cost-benefit analysis for your application.
How to handle curved surfaces?
Specialized gun adapters maintain perpendicularity on radii down to 50mm.
Are there material thickness limits?
Our record: 0.3mm titanium foil. Consult engineers for extreme applications.